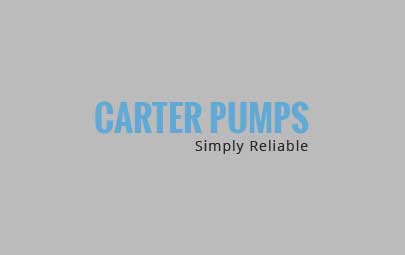
The pump can be seen to be the heart of a pressure washer system and is also often the most neglected component in the system. It is forgotten as long as it is working, but once it fails, it has the highest priority. Anyone who tries to repair a pump or a washer system should have the proper training to do so, and there are many free technical training programs offered by manufacturers to authorized distributors or dealers. Nevertheless, it is also good to read up and get a basic understanding of how to maintain high-pressure plunger pumps.
Common Points Of Failure
There are two most common ways in which a pump could fail. Firstly, normal maintenance efforts may have been neglected, such as changing the oil regularly, checking that the o-rings are not damaged, et cetera. Typically, these can result in issues like the pump running with water in the oil, running with leaking or worn packings, or broken plungers, which can all destroy the pump.
Secondly, poor inlet conditions may also lead to other troubles such as dry running, cavitation and poor filtration or wrong filtration used. These may, in turn, lead to premature packing, as well as damage to the valve and plunger.
While these may be the most common issues, it is important to note that maintenance does involve checking every single component in the pump system, and not just these few commonly problematic ones. This article will provide you with ways in which you can carry out these maintenance efforts.
Daily Checklist
One way is to put together a daily checklist, which should include all the vital components of the pump system. Such checklists may also be offered by equipment manufacturers on their websites. Some examples of components to check are water supply and pump (check for leaks), engine (check the oil level, gas, and air filter), drive system (check belt tension and pulley system), hose, spray gun, lance, and nozzle. Once all these have been checked, start the system and test it again under pressure to look for leaks, and ensure the entire system is working properly, without telltale weakness symptoms like excessive pressure or vibration.
Preventative Measures
Other things to take note of include the schedule for changing oil. Pump manufacturers usually recommend the oil be changed after the first 50 hours of operation. Subsequently, it should be every 500 hours, or three months, whichever comes sooner. For pumps undergoing very heavy usage or severe conditions, the oil may have to be changed sooner. The type of oil needed may also depend on the pump you purchase, as there are certain oils that perform best with certain pumps. Another thing you must consider is the wearing down of certain components such as packings, brass retainers, valves, plungers, and intermediate ring guides. It’s best to check the estimated lifespan of each of these components so as to replace them ahead of time before they cause a system breakdown. The pump is usually one of the most important components in a pressure washer system. For expert advice and proficiency in installations or replacements, speak to a professional at Carter Pump today.